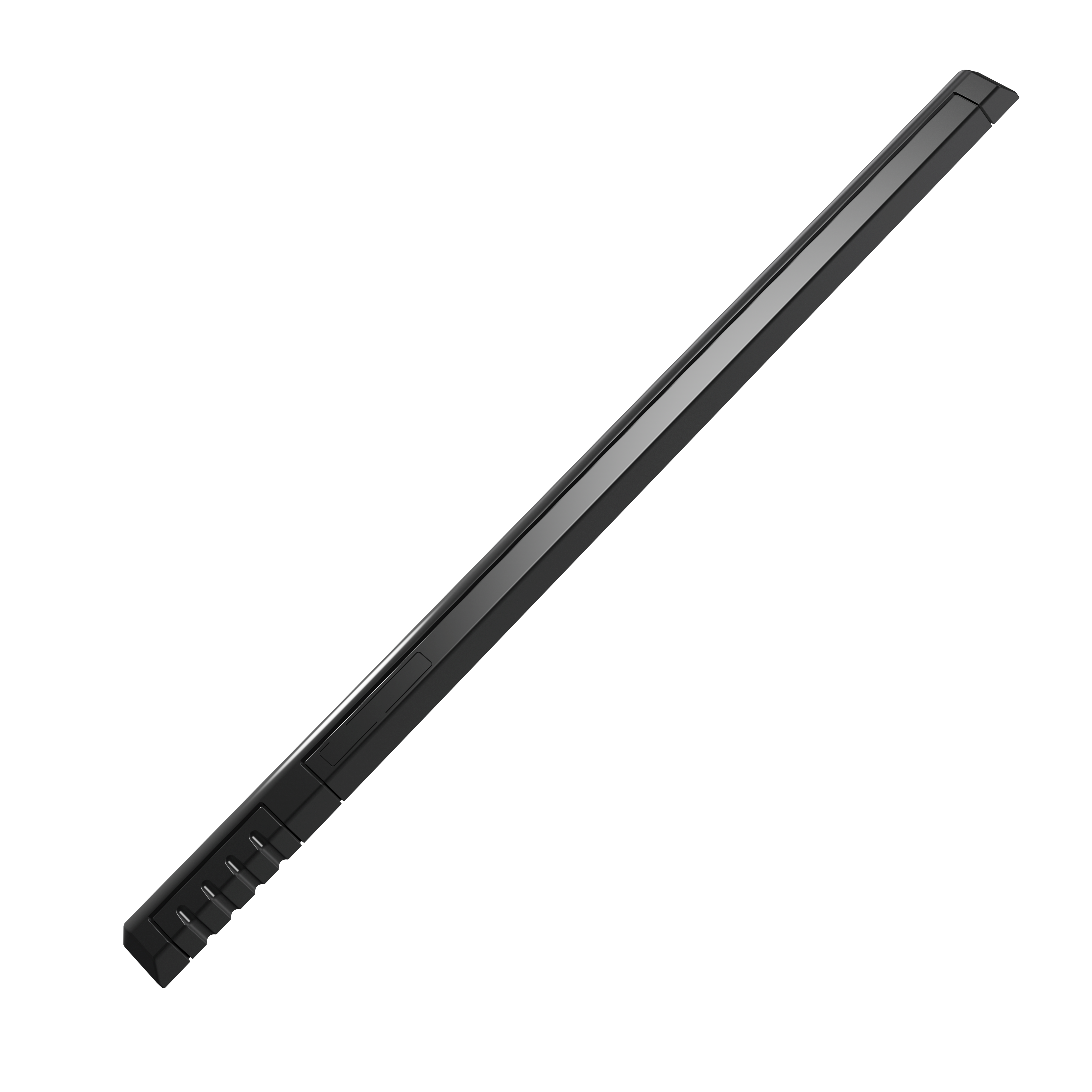
2K TOOL BOX BUMPER
TRUSTED E-MULTI PLATFORM SELECTED FOR PRECISION PRODUCTION OF CHALLENGING, LARGE MULTI-MATERIAL PART
Core Technology Molding Corporation, out of North Carolina, is a company that provides integrative and innovative plastics solutions to the world’s leading companies. They are known for excellence in the manufacturing of highly engineered plastic products that have tight tolerances, require sophisticated tool designs and mandate efficient manufacturing like 2-shot injection molding.
They offer a wide range of solutions which includes injection molding and specialty molding processes. They have worked with almost every plastic resin in the industry. Applications using engineering resins such as polycarbonate, nylon, ABS, PC/ABS blends, polyester, acetal, and reinforced grades are their specialty. They currently employ three certified Master Molders to develop robust injection molding process, using the techniques of scientific molding and scientific processing. Scientific principles related to the complete molding process, from drying the resin to the shipping of the finished product are utilized.
Core Technology Molding Corporation offers a handful of specialty molding processes including: 2-Shot, over-molding, and insert-molding. Some of the benefits include cycle time reduction, lower tooling costs, resin savings, improved part quality, stress reduction and the ability to use smaller tonnage presses for the molding process. Their customers include well known major brands from a variety of markets which includes medical, automotive, packaging, outdoor power equipment and more. They also operate the non-profit “Molding Kids for Success”. A STEM education program to showcase the industry and illustrate that plastics can be fun.
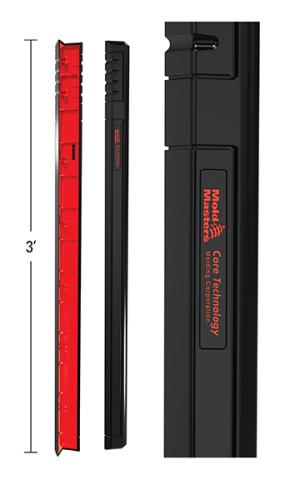
Core Technology Molding Corporation was presented with an opportunity to mold a challenging plastic bumper component for a large rolling automotive mechanic tool box cart for a well known American industrial tool brand. The component had high finish and surface quality requirements. It was about 3’ in length, incorporated multiple colors and required a crisp, sharp imprint of the company brand (including the small trademark icon). Its design called for it to be produced using a red colored Nylon substrate over molded with soft black rubber. Not many molders in the Southeastern United States do 2-shot in the medium tonnage range.
To meet this demand, Core Technology Molding Corporation became the first to purchase Mold-Masters new largest format E-Multi auxiliary injection unit (EM5). The E-Multi was used to inject the Nylon substrate (red color) while the black over molded runner was injected by the machine’s primary unit into the parts 2+2 mold. Their experience and success from a previous small scale automotive application made selecting the E-Multi platform for this application a no brainer.
The motto of Core Technology Molding Corporation is “To Market Faster”. Compared to a lead time of 52 weeks for a multi-shot injection machine, E-Multi’s 10–12-week standard made things so much faster. The speed of implementation was also aided by E-Multi’s plug and play capabilities. From a cost perspective, E-Multi also presented a major advantage. Core Technology Molding Corporation calculates that savings were about 30% compared to a custom multi-shot machine. E-Multi was also a better option based on adaptability. Six different tools could be run on a single machine with the E-Multi which otherwise would have required the use of two different injection machines.
Core Technology Molding Corporation was able to meet the production challenges and produce high quality parts with excellent surface finish and crisp logo imprints. In fact, the molded component was so well received that it was highlighted at a convention hosted by their customers promoting new products.
As an early adopter of new technologies that allow them greater flexibility, Core Technology Molding Corporation is ready to handle any application and answer the call for customer production requirements. As a result, they have already been able to leverage this application success and flexibility to capture market share from larger competitors and satisfy the production requirements of larger customers.
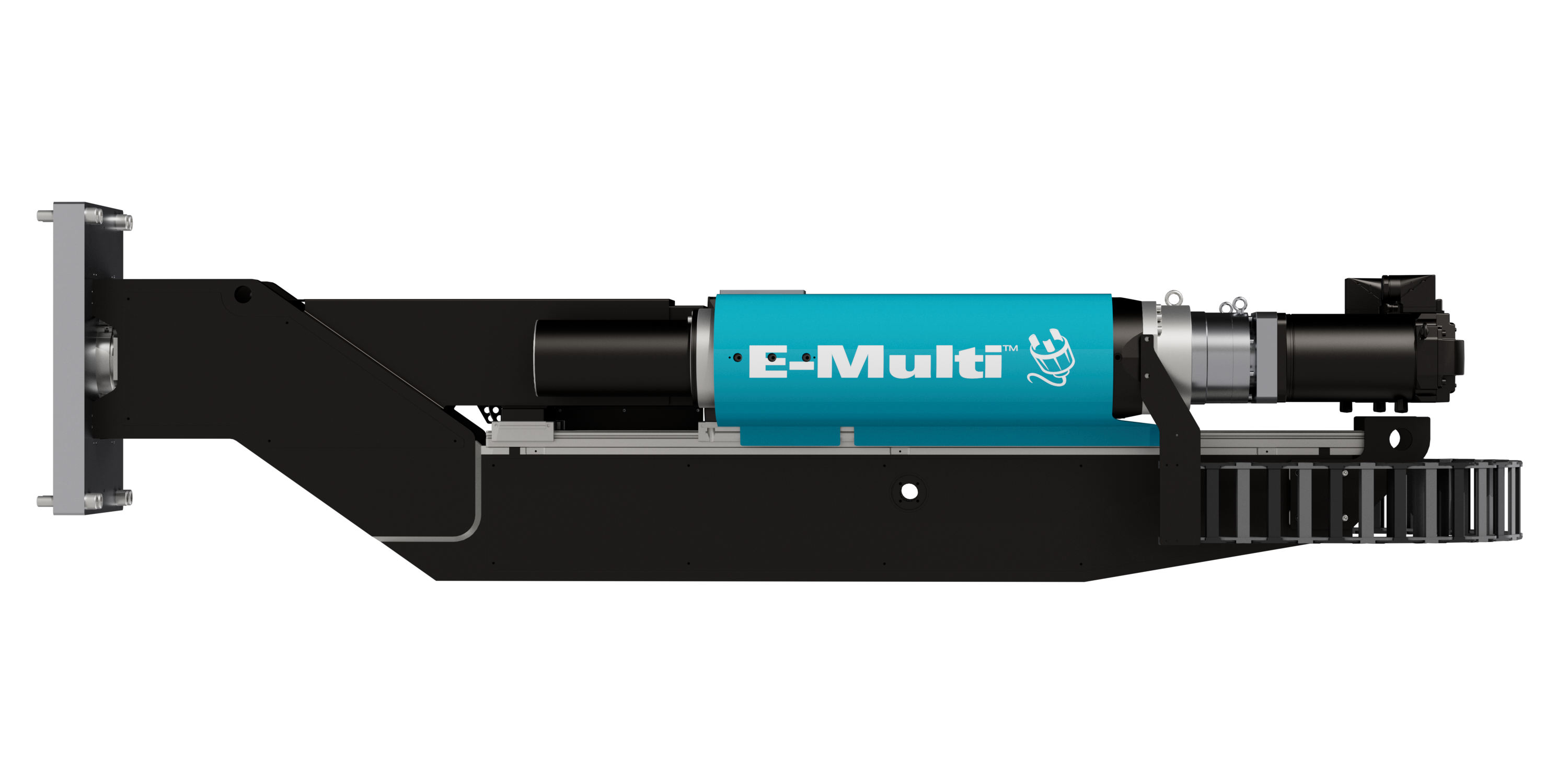
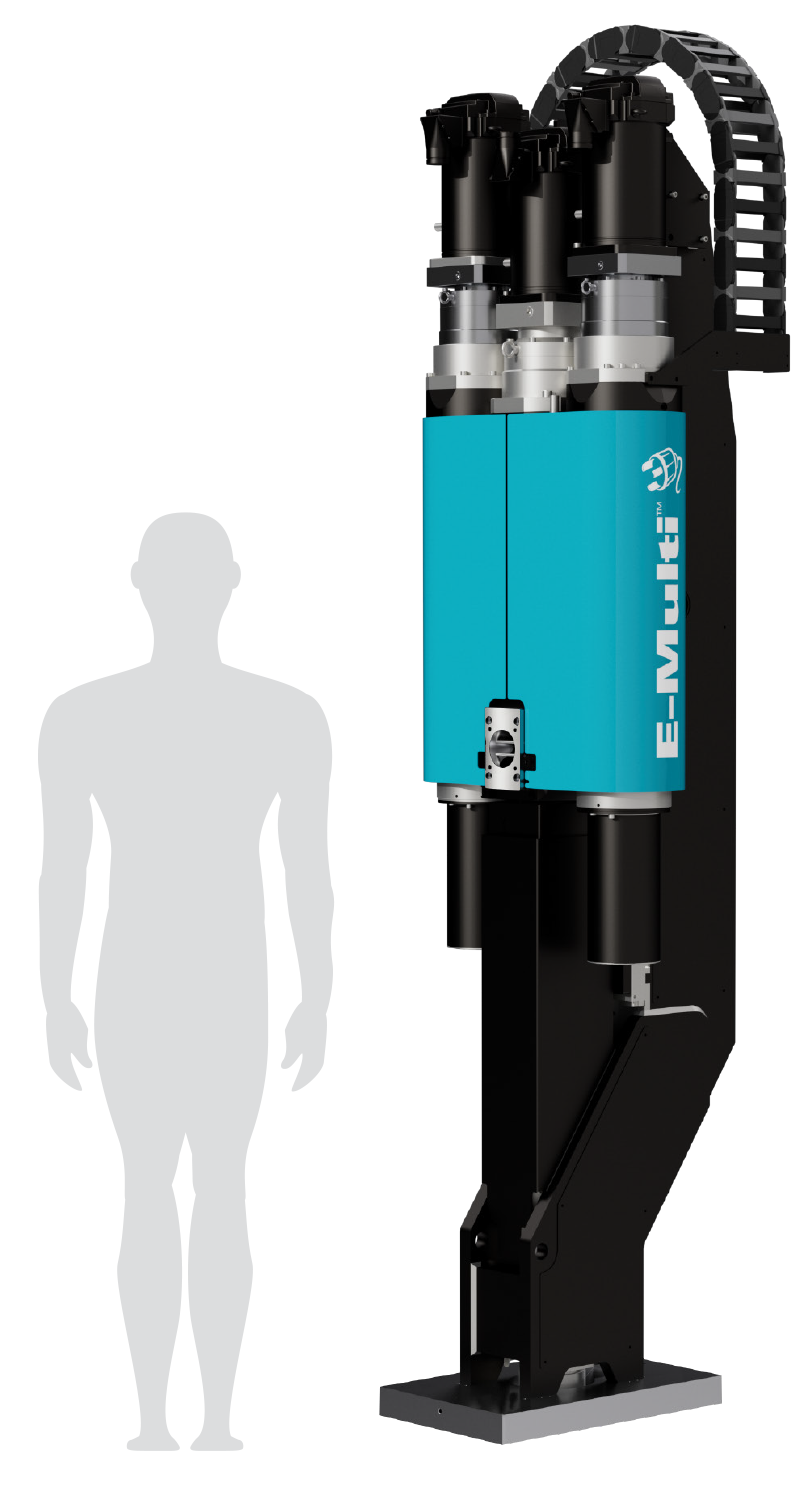
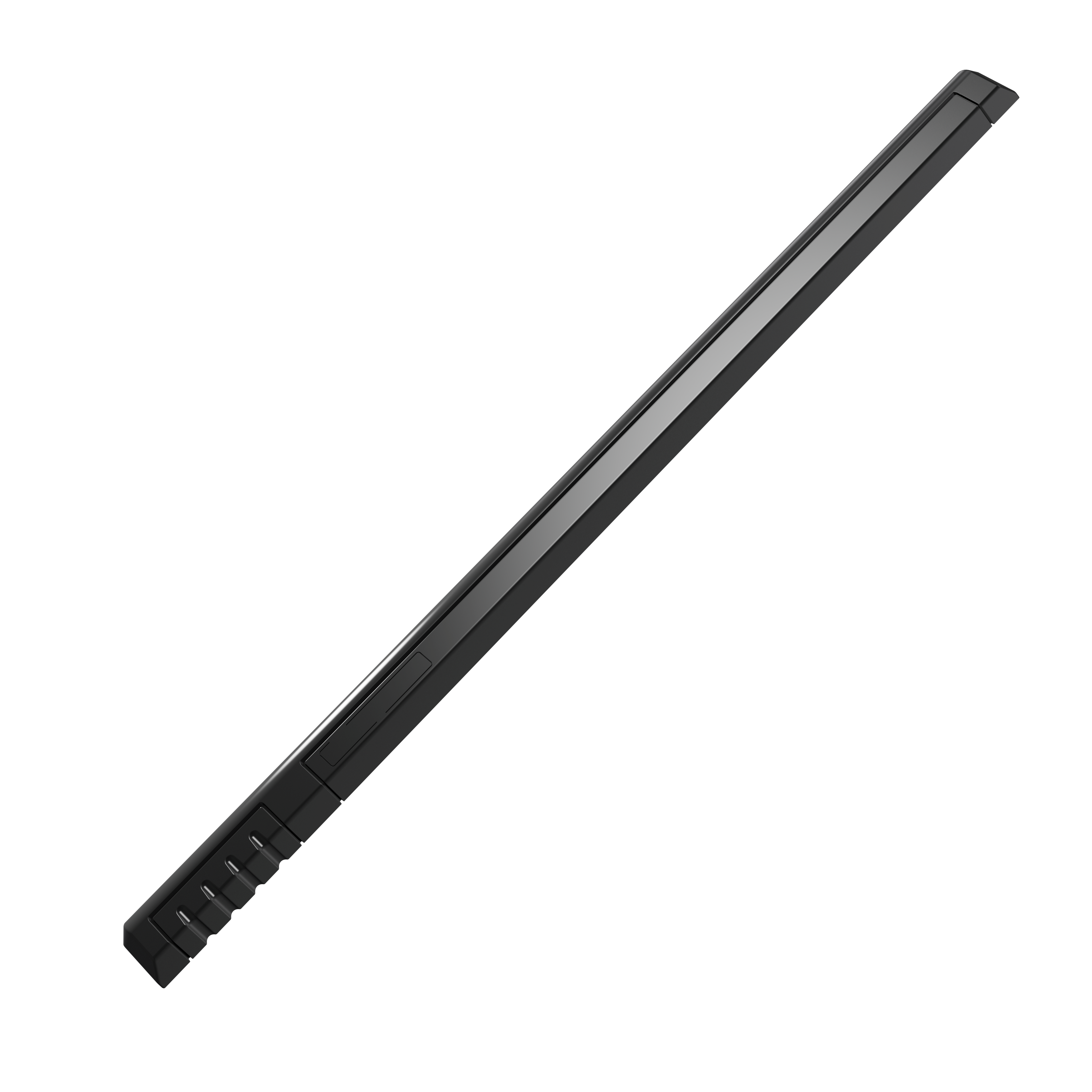
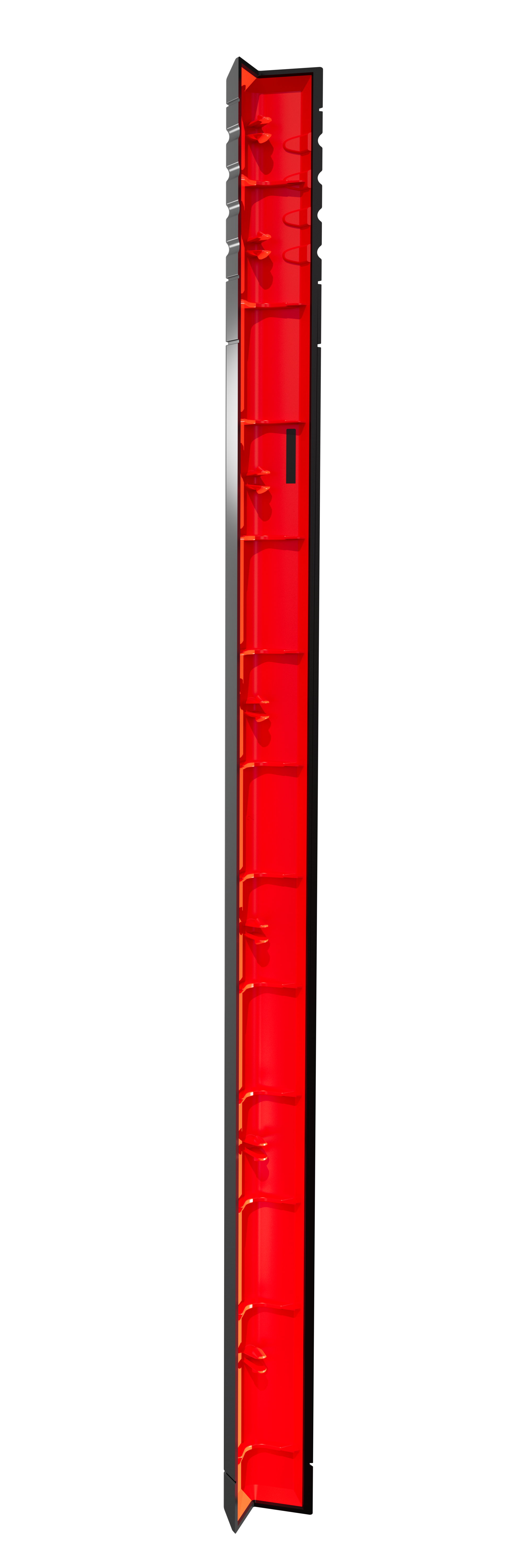