Mold-Masters is trusted by many global electric vehicle brands and component suppliers. Molding components for EV's often have their own unique set of demanding applications that involve complex parts and challenging hard-to-mold polymers. Common applications associated with electric vehicle (EV) drivetrains include electric motors, batteries, connectors, power control units, thermal management systems and more. Our supercharged EV molding solutions enhance molded part quality, increase productivity and minimize scrap.
Requirements
MM Solutions
Case Studies
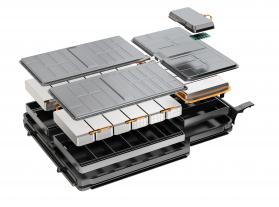
Li-Ion Battery Cover
SUMMIT-SERIES INCREASES UPTIME BY 400%+ IN CHALLENGING PFA BATTERY APPLICATION
A new customer approached us about molding Li-ion battery covers to meet the growing demand from the electric car industry from a challenging PFA resin. This special resin is important to this application as it’s resistant to corrosion from the battery fluid and it prevents the battery from overcharging. Traditionally, components made from this material have been produced using cold runners. However, as the material is very expensive, the customer was hoping to transition to hot runners in order to lower their scrap and production costs.
The demands of molding with a PFA resin makes it a challenge for any injection molder. The major issue with this resin is that during the heating process the material releases a fluorine gas that is corrosive to steel. Both hot runner system and injection molding machine are affected by this gas. Once the corrosion starts it spreads rapidly and leads to valve pin seizure and eventual leakage. Before approaching Mold-Masters the customer had tried working with several other hot runner suppliers who all failed. Their systems would only operate for a week and then require extensive repairs and cleanup maintenance. This was not a sustainable practice, so the customer continued their search for a better solution.
This fantastic opportunity involved Mold-Masters collaborating closely with the customer in order to ensure their application was successful. Mold-Masters Summit-Series hot runner system is specially suited to such applications as it is intended to accommodate challenging resins that are corrosive/abrasive or have temperature/shear sensitivities. Summit-Series incorporates a variety of special materials and coatings into its components that protect the system from harmful corrosive materials in order to extend service intervals.
By utilizing Mold-Masters Summit-Series hot runners uptime was increased by at least 400% compared to the competition (1 month vs. 1 week). If the mold remained in continuous production, some Summit-Series systems have been able to remain in production for up to 12 weeks (1 million cycles) significantly extending the time between service intervals and unscheduled downtime. This customer was very pleased with the results and now relies on Summit-Series hot runner systems for this application.
The Mold-Masters Summit-Series hot runner system offers a clear competitive advantage for PFA applications. This success will surely transition more manufacturers to Summit-Series on PFA applications that ultimately pays for itself through increased uptime and reduced scrap.