Innovative and unique packaging for niche items that stand out from their competitors while getting to the market quickly at an affordable cost defines the packaging industry. Common applications include small in-mold labelled containers to large pails, cosmetic jars, single use coffee capsules and more.
Requirements
- Part weights range from 15g - 500g (typical)
- Thin and thick wall designs
- High injection pressures
- Aggressive L/T ratios
- Fast cycle times
- Low cavitation
- High productivity
- High reliability
- Extending product shelf life, freshness and flavour of products
- Design differentiation options
- Sustainability (Bio-Resins & PCR)
Common Resins
MM Solutions
Case Studies
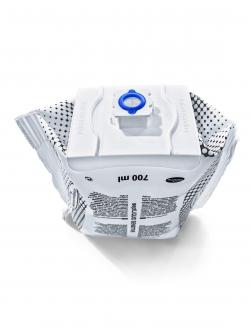
Multi-Material Hand Sanitizer Packaging
RAPIDLY AND ECONOMICALLY INCREASE YOUR CAPACITY TO MEET GROWING DEMAND WITH E-MULTI.
Founded in 1971, Hagleitner Hygiene International GmbH has specialized in innovative hygiene solutions. Their product assortment ranges from soap and disinfectant dispensers to dosing system for washing and rinsing systems through to highly effective cleaning agents. The family company manufactures all products itself. The headquarters in Zell am See, South of Salzburg, combine chemical-technical production, paper finishing and plastics processing.
Hand sanitizers have been among the most popular products since the beginning of the corona pandemic. Dispensers are not only standard in hospitals and care facilities but also now in many public, retail and office environments. Companies offer sanitizers for their employees and visitors as a measure to help prevent the spread of COVID-19. In order to be able to quickly and easily refill the contactless dispensers, Hagleitner has developed refill “vacuum bags”. These refill packs each consist of a tubular bag and an adapter piece with an integrated closure. Inserted into the dispenser upside down, the closure slides open automatically.
The adapter piece, which incorporates an integrated seal, are produced using a two-component injection molding process in a 4+4 turntable mold. First, the shoulder plates made of white polypropylene are injected and after the tool rotates, the blue TPE seal is injected directly onto the part. Prior to COVID-19, Hagleitner produced 10,000 refill packs a day on a single machine (20hr/5days).
In order to service the skyrocketing orders, the Austrian hygiene specialist had to more than double its production volume in less than a week. There was no way to meet the increased demand by simply increasing production on the existing molding cell so a second molding cell needed to be launched. This record-breaking implementation speed was made possible, in part, by Mold-Masters E-Multi Auxiliary Injection Unit which allowed them to convert one of their existing single shot machines over to this multi-material application. Almost overnight, production was increased to 15,000 units per day (24hr/7days) with these two molding cells.
Hans-Jürgen Landl from Hagleitner stated that the cooperation with Mold-Masters is excellent, especially with the local representatives in Austria. “This is truly a lived partnership”.
The Mold-Masters E-Multi Auxiliary Injection Unit is a proven platform, utilized globally, that easily and economically converts any injection machine to multi-material capabilities. It can be installed horizontally, vertically or any position in between. It’s also compatible with a wide range of thermoplastic and LSR materials. As it is electrically powered, it maintains a much more compact work envelope than hydraulic alternatives and its servo motors allows for production to be highly precise, repeatable and reliable. They also have the ability to be utilized throughout a production facility or shipped from location to location with relative ease. Hagleitner were already utilizing several E-Multi units on their existing cells for years so they were already familiar with all of the benefits. Although E-Multi’s have been supplied in as little as 5 weeks (much faster than a new injection machine), obtaining one within a week when they are not off the shelf products, posed it’s own challenge.
To the credit of Hagleitner’s strong partner network, they realized their supplier (who supplied them with canisters and bottles for many years) had identical E-Multi units in their own plants. Working together, the supplier sent this piece of equipment over for the conversion to take place. Hagleitner brought their duplicate back-up mold into full time production as part of the second cell. The rest is history. In only a few days, production was increased to 15,000 units per day (24/7) with these two molding cells.
With the E-Multi, we are more flexible than with a second fixed injection unit on the injection molding machine and it can also be integrated quickly into any other injection molding machines. The necessary requirement for this is of course the appropriate equipment with the corresponding interface. - Hans-Jürgen Landl, Hagleitner
This is one of the many examples of how Mold-Masters product advantages were leveraged to pull off what would be impossible for others. Mold-Masters is proud that our customers where able to utilize our products as part of their solution towards the global fight against COVID-19.
If you’re in need of a similar solution please feel free to reach out to Mold-Masters today https://www.moldmasters.com/form/contact-us
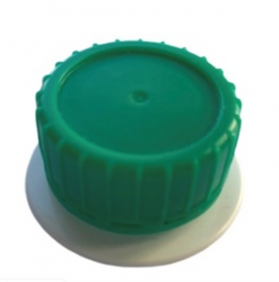
Complex Carton Style Closure
STREAMLINE PRODUCTION TO MAXIMIZE PRODUCTIVITY WITH E-MULTI
“The E-Multi’s precise shot weight and repeatability was a critical component to the success of this application”
- Roberto Silla, President, EasyPlast (EU)
EasyPlast, a European based company, has been manufacturing molds and molding plastics since 1994. It specializes in multi-cavity molds for consumer products and in molding parts in PP, LDPE, HDPE, and LLDPE. Available components include caps, capsules, dispensers, ferrules, medical, houseware, packaging and more. The company manufactures over a billion molded items every year. EasyPlast is proud to create products of the highest quality for national and international markets.
EasyPlast was producing a complex Carton style closure (HDPE 3-component screw cap, 2 -color). The current process involved molding each component in 3
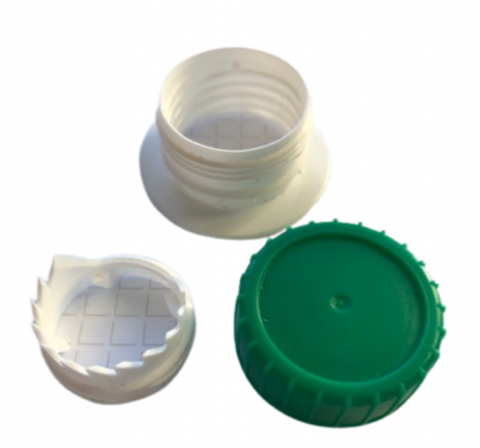
separate cells with 3 separate molds. This specific closure design incorporates a cutter element that opens the aluminum seal once the closure is opened by the consumer.
As part of this process, from the mold(s) they are removed by robot to an assembly jig where the caps are finally ejected fully assembled.
EasyPlast was hoping to improve the manufacturing process to improve overall productivity and efficiency to lower part cost by:
- minimize equipment utilization and manpower
- improving part quality
- Reducing cycle time (and handling)
- saving floor space
EasyPlast had developed a unique 24+24+24 triple stack family mold and ultimately patented the technology. As a component of this solution an E-Multi (EM4) auxiliary injection unit and controller was utilized to inject the component with the 2nd color.
The E-multi unit was mounted in a horizontal configuration almost parallel to the press (15° angle) utilizing a floor stand. The E-Multi unit was selected for its precision injection capabilities, repeatability, reliability and shot capacity.
The customer estimates that the time to complete the injection and assembly process has been reduced by about 50% as a result of this new system. The shrinkage occurs to all three parts evenly after assembly leading to extremely high tolerances and excellent part quality. As a result of minimizing the handling requirements after molding, the scrap rate has been reduced by up to 75% (was 2%, now 0.5-1%). Overall, the customer reports that this new process has enabled him to lower part costs by about 40% and predicts annual savings of at least €100k. The customer attributes these savings to the more efficient process (enabled by the E-Multi and special mold design) which requires 1 less person, 2 less molding machines, less cooling equipment, lower production times, lower assembly times, lower scrap rate and lower energy consumption.
In addition, EasyPlast expects to be able to further improve cycle times as the E-Multi has not been utilized to its full performance limit (it is not the bottleneck in the production process).The controller is also favored for its interface, ease of use and installation.
The customer was very happy with the unit as it's working extremely well. There are plans to order another unit for a future (similar) project.
If you’re in need of a similar solution please feel free to reach out to Mold-Masters today https://www.moldmasters.com/form/contact-us