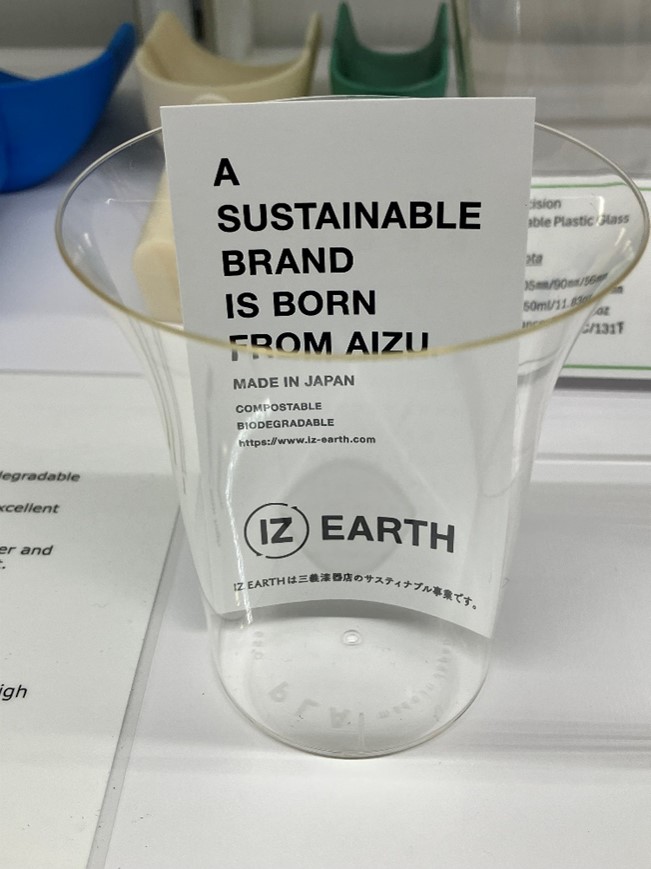
PLA Bio-Degradable Transparent Cup
MOLD-MASTERS HOT RUNNER SYSTEM PLAYS CRITICAL ROLE IN PRODUCING THE WORLDS THINNEST INJECTION MOLDED 100% BIO-DEGRADABLE TRANSPARENT CUP
Sanyoshi Lacquerware (Aizuwakamatsu City, Fukushima Prefecture, Japan), a packaging company, was looking to produce a transparent cup made of 100% polylactic acid (PLA). This multi-use cup is biodegradable at the end of its life as PLA converts into water and Co2 in soil when conditions are right.
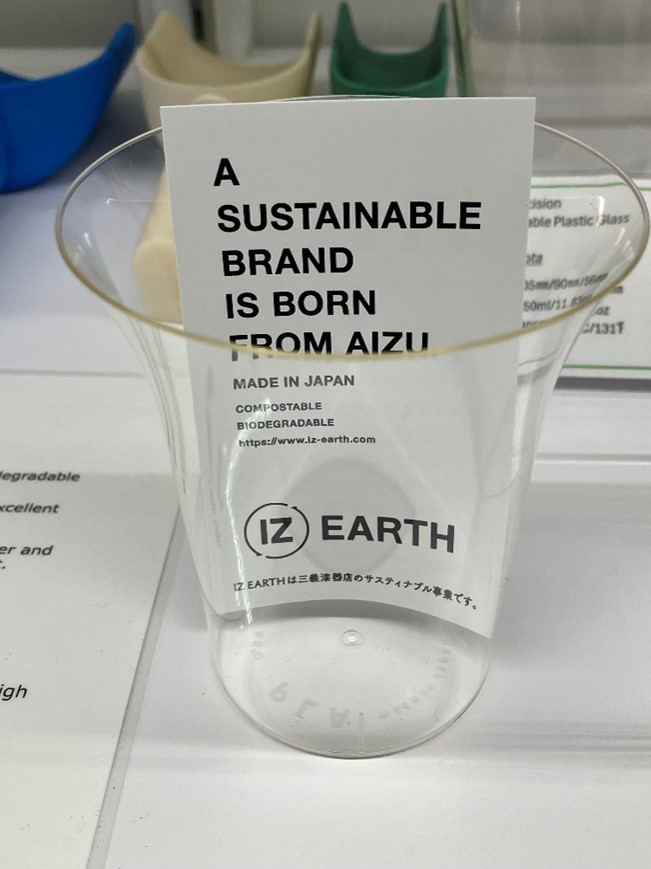
PLA is typically processed at low temperatures and is a thermally sensitive material. It requires stable temperatures from the hot runner system to process effectively. In addition, PLA is typically a corrosive material that can degrade system components over time. Failure to overcome these limitations often results in processing and part quality issues that can appear as visual defects and discoloration. The additional challenge with injection molding PLA in a thin wall application is that PLA is a difficult material to inject into every corner of the mold due to its high viscosity. Also, using PLA has higher material costs compared to conventional resins.
Mold-Masters Summit-Series hot runner system was selected for its ability to accommodate the materials thermal sensitivities and corrosive characteristics. Summit-Series offers our most precise thermal profile and incorporates more durable higher-grade steel along with special coatings to enhance durability and minimize the effects of corrosion to the system. In addition, to mold thin-walled products, a special internationally patented injection process, held by KOMATSU & ASSOCIATES in Japan, was used which involves dissolving a large amount of supercritical Co2 in the PLA to increase its fluidity. The president, Mr. Michio Komatsu, was awarded Prime Minister’s Award of Japan’s Manufacturing Grand Award by Mr. Shinzo Abe for his extensive PLA injection technologies and is a technical advisor for Mold-Masters in Asia. Although PLA is more expensive than general-purpose plastics, making it thinner has made it possible to reduce costs by reducing the amount of material used. Costs have been reduced further through mass production. An 8-drop mold creates 8 cups with each cycle which helps increase productivity to lower cost per part and gives them the potential to produce tens of thousands of cups a day with each mold.
The Summit-Series hot runner system in combination with the special patented injection process allowed them to produce a thinner-walled molded part than ever before (0.53 mm). Sanyoshi Lacquerware (Aizuwakamatsu City, Fukushima Prefecture, Japan) now offers a 0.53mm thick transparent cup made of PLA. They claim "0.53 mm is the world's thinnest, thin-walled plastic cup made by injection molding of PLA." Not only are they able to mass produce these cups economically, but when these cups reach their end of life, the thinner wall design allows these cups to compost very quickly. It is said that under the ideal conditions, these cups can fully decompose within 30 days. PLA thin-walled cups molded using this technology are expected to go on sale in the summer of 2024 under the brand name “IZ EARTH”.
“Mold-Masters Summit-Series hot runner system played a critical role in allowing us to push the boundaries of what’s possible in this application.”
Mr. Komatsu
To learn more about our bio-resin & PCR processing solutions and how they can benefit your application please speak with your local Mold-Masters technical expert today.