Understanding Differences in Hot Runner Heater Technologies – Nozzles
All hot runner systems need a heat source to operate as designed, however not all hot runner systems use the same heating methods. The type of heater technology your hot runner system uses can significantly affect molding performance, part quality, and system cost. No heater method exists that is ideal for every scenario and each one has their own pros and cons but illustrating their differences may help you in understanding your hot runner system a little more and give you a bit more insight on your next purchase. Some hot runner systems may use a mix of heating methods depending on the components of the system and application but for the purposes of this discussion we will focus on nozzle heater elements.
The main types of nozzle heating methods include Embedded Heat Sources (Brazing) or External Heat Sources (Sleeves and Coil). Selecting the right heater element is always a careful balance of performance, reliability, and cost (both initial investment and operating). Many factors are also weighed including industry, mold design, part variables and production requirements.
EMBEDDED HEAT SOURCES
Embedded Heaters are generally ideal for nozzles with lengths less than 500 mm (with exceptions).
- Greater flexibility for optimization through Computer Aided Engineering (CAE) analysis for enhanced thermal profile
- Greater heat transfer efficiency than external heat sources (higher contact area)
- Won’t shift preventing cold spots that would affect production quality
- Helps protect elements from physical damage
Brazed-In Heaters
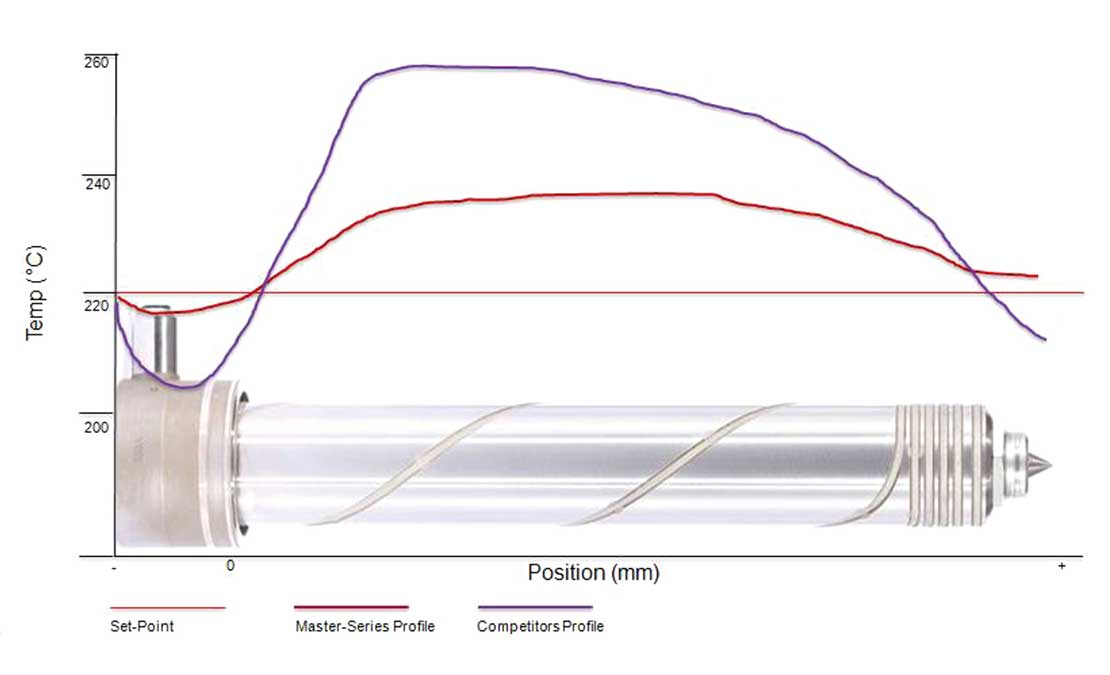
Brazed-in Heaters generally offer the best performance and reliability making them ideal for achieving the highest molded part quality and long-term production. Using advanced CAE analysis, heater channels are tailored to optimize the thermal profile of each nozzle for unbeatable precision. The result is superior part quality through enhanced shot-to-shot and drop-to-drop consistency.
Brazing also completely eliminates any air gaps that can lead to heater failure through electrical arcing. Brazed heaters are often made to higher quality standards than other heaters and therefore have a very low failure rate. With a lifespan able to exceed 10 years, they have the ability to outlast the life of the mold. While brazed heaters require a higher initial investment this is typically offset by higher quality part production, eliminating heater replacement costs and minimized downtime. Part quality aside, the higher the cavitation and longer the production run the more it makes sense to invest in Brazed heaters.

EXTERNAL HEAT SOURCES
External Heaters (Sleeves & Coils) are generally ideal for nozzles with lengths greater than 500 mm (with exceptions).
- Lower cost for more economical system pricing
- Ability to stack up to 3 heaters on nozzles with longer lengths for enhanced temperature control of multiple zones (difficult to accurately control a long nozzle with a single zone - too many variations)
- Higher standardization allowing for easy global access to spare parts from multiple sources
Heater Band Sleeves
As an external heat source, Heater Band Sleeves are sleeves with heater elements embedded into them. These sleeves slide overtop a nozzles core, are secured in place with a retainer (pin or circlip) at the nozzles tip and the full length of the sleeve is heated to help maximize heat transfer. While not as ideal as Brazed elements, they offer optimized element channels which generally perform better than traditional heater coils given the typical application (large parts-automotive).
In addition, because the elements are embedded in the sleeves a more uniform heat profile is achieved and any problem associated with shifting is eliminated. Replacing heater elements in the field, especially on longer nozzles is fairly quick and easy, as the sleeves just slides off the nozzle core once the retainer is removed.

Heater Coils (Traditional)
Heater coils are generally the most popular heating element of any type of hot runner system due to their very low initial cost and widespread global availability. This makes them ideal for creating economical hot runner systems with easy to source spare parts. Generally speaking, heater coils are ideal for low cavitation hot runner systems producing simple cost sensitive parts and/or limited production runs or hot runner systems with extended nozzle lengths that benefit from having multiple zones (automotive). When used on longer nozzles they can be more difficult to install/remove as they can be tightly coiled around the nozzle so they don’t slide off like heater band sleeves.
Because these elements are installed directly over top of the nozzle core, they operate with a very limited contact area which restricts heat transfer efficiency and requires more energy to operate. As there is no optimization possible with standard off the shelf components, the thermal profile is often more challenging to control and have the least precise thermal profiles due to thermal inconsistencies. The gate area temperature may not be as hot as the body since the heater band cannot run the full length of the nozzle as embedded elements can.
Depending on the manufacturer, heater coils may also require larger cut-outs to accommodate their external design and sometimes larger terminal ends and clamping mechanisms. In addition, they generally have the shortest lifespan of any heater type and usually require replacement within 1-3 years so spare part and downtime costs can quickly eat up any upfront savings from an initially low system cost.

Mold-Masters has been manufacturing the industry’s leading hot runner and temperature control systems since 1963. Mold-Masters designs, manufactures, and supports a full range of hot runner products, including hot runner systems, temperature controllers, hot halves, and gating technologies.
*The content in this article is to be used as a general guideline only. Hot runner manufacturers may have significant differences in how they implement each type of heating element. Speak to your hot runner supplier for more details.